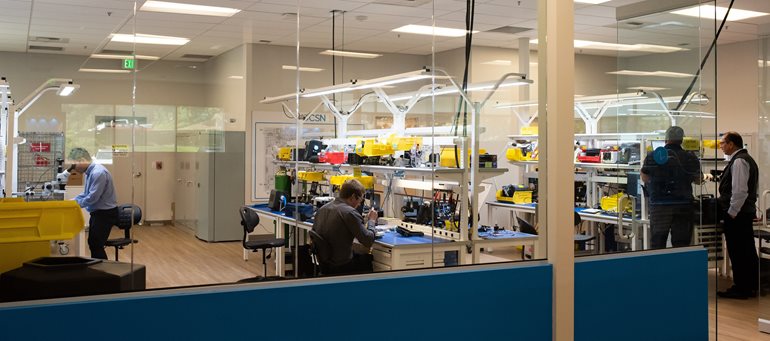
By Douglas Esser
Ventec Life Systems is a medical device company in Bothell, Washington, that makes ventilators — the machines that support life for people who lose the ability to breathe on their own due to injury or disease.
When the coronavirus pandemic hit, demand rocketed. Suddenly, Ventec was in national headlines, partnering with GM to vastly multiply its production, using a former auto electronics plant in Kokomo, Indiana.
Working under intense pressure, mechanical engineering graduates and an intern from the University of Washington Bothell are among the employees helping Ventec rise to the challenge of increasing production from 200 machines a month to 10,000.
Prepared to pivot
While nothing could really prepare anyone adequately for such a crisis, the graduates and intern said the college experiences they found most useful were the hands-on projects and experiential learning capstone courses they had under School of STEM faculty members, including Professor Pierre Mourad, Associate Professor Steven Collins, Associate Professor John Bridge and former staff member Ivan Owen, who managed UW Bothell’s Makerspace lab.
Andy Chapman (Mechanical Engineering ’17), Luke Johnson (Mechanical Engineering ’16) and Christopher Sohlberg (Mechanical Engineering ’17) all have worked long hours in Kokomo, helping autoworkers make ventilators. Still at UW Bothell, intern Caleb Taing, has been supporting the work at Ventec in Bothell.
5 in 1 life support
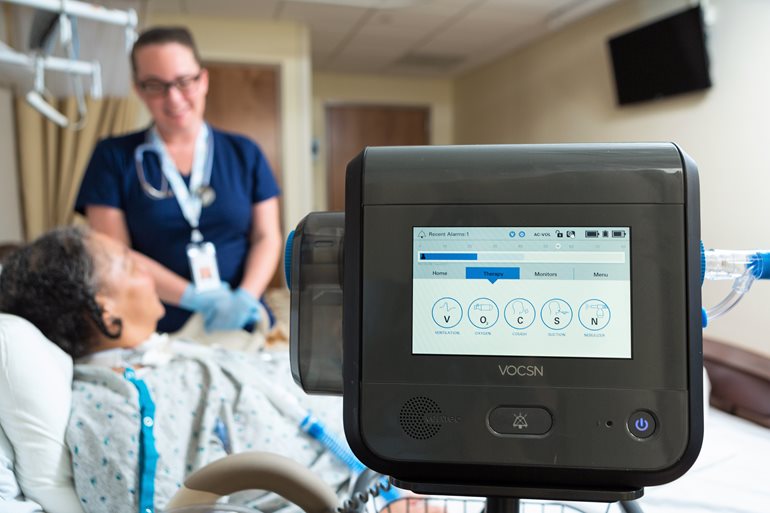
Ventec’s now highly prized device received FDA approval in 2017 and went into production in Bothell in 2018. It combines a ventilator with four other related functions that in the past have required separate machines: an oxygen concentrator, cough assist therapy, suction tube for secretions and nebulizer to deliver drugs in the form of vapor.
The device, VOCSN, takes its name from the five functions — ventilator, oxygen, cough, suction and nebulizer. Ventec founder Doug DeVries invented it because his father was an ALS patient who was put off by all the machinery, tubes and wires it would have required at that time. (Amyotrophic lateral sclerosis is often called Lou Gehrig’s disease.)
In one 18-pound package, the VOCSN has a touch-screen control designed to be as easy to use as a mobile phone. The device can attach to a stand, bed or wheelchair. It also can be used anywhere from an intensive care unit to a home.
Tens of thousands of people rely on ventilators to live: people with ALS, muscular dystrophy, spinal cord injuries and advanced COPD (chronic obstructive pulmonary disease), said Chris Brooks, Ventec chief strategy officer.
Supply and demand
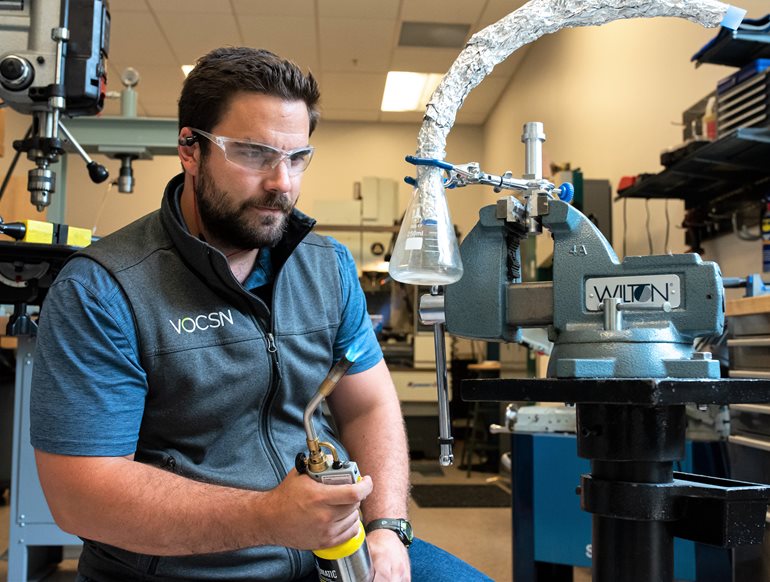
In recent months, ventilators have also become a critical care device for patients in full advanced respiratory distress from COVID-19.
Among about a dozen ventilator makers in the world, Ventec was beginning to grow its market share, Brooks said, when it saw what was happening in China and then in Kirkland, Washington, where a COVID-19 outbreak in the United States was first reported.
“We knew the demand for ventilators was going to well exceed what any individual manufacturer could make,” he said.
Soon, it was not only doctors and respiratory therapists calling to say they needed more ventilators but governors and ministers of health, too. There also were calls from corporations offering support. GM said it could help with the supply chain.
The multi-purpose VOCSN may be a single device, but it has 700 parts.
On to Kokomo
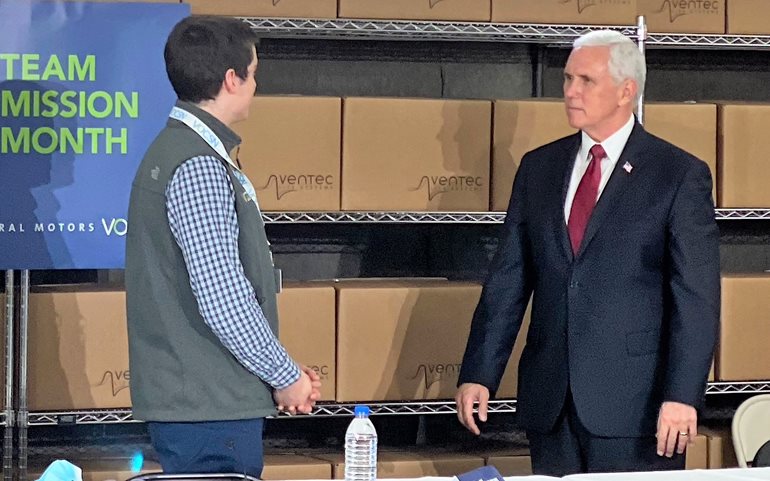
Andy Chapman with Vice President Mike Pence
GM and Ventec executives had their first conference calls on March 17. Ventec CEO Chris Kiple and GM agreed March 27 on a partnership to use 1,000 GM employees at Kokomo. On April 8, the U.S. Department of Health and Human Services awarded a contract under the Defense Production Act to build 30,000 VOCSN V+Pro critical care ventilators by the end of August. On April 17, the first ventilators from Kokomo were delivered to two Chicago-area hospitals.
And, on April 30, Vice President Mike Pence, as head of the White House coronavirus task force, toured the Kokomo plant and met with executives and workers including Ventec CEO Kiple and engineer Chapman. Pence said it was extraordinary to see what had been accomplished in one month.
“To see the way this team has responded here in such a short period of time I know is an inspiration to everybody on our team. I had to check the dates again,” the vice president said. For the “ingenuity, the creativity, the hard work,” he said. “I want to say thank you.”
To speed up production and reduce cost, the ventilator built in Kokomo — the V+Pro — is a simplified model without the cough, suction and nebulizer functions. In addition to the contracted 30,000 units, the goal is to make many more as soon as possible for national and international needs, Brooks said.
Until there is a coronavirus vaccine or a cure for COVID-19, Ventec ventilators will likely remain in high demand.
“We pride ourselves on medical device quality, and that’s first and foremost,“ Brooks said.
From the biotech innovation zone
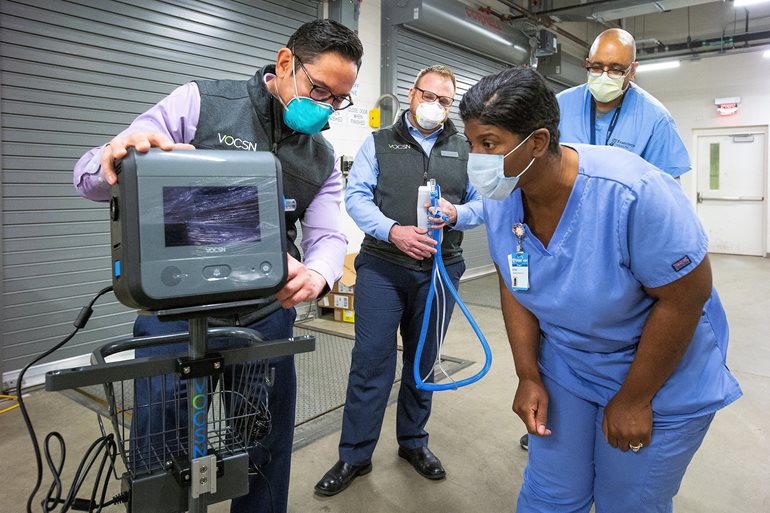
Among the reasons Ventec is located in Bothell is the city’s biotechnology innovation zone — and the UW talent, Brooks said.
“Certainly, we’re able to recruit great talent in the area from manufacturing to engineering to design. A lot of that is feeding out of the UW system and UW Bothell obviously being in our direct backyard,” Brooks said. “That’s part of why Ventec is here and how we’ve been able to be successful, with the talent from the local community.”
Increasing production by 50 times at a different manufacturing location in one month is unprecedented, Brooks said. “It’s been exciting to see everyone step up as a leader and be that expert who transfers that knowledge to folks who a few weeks ago were building cars.”
Ventec is smaller than most medical device companies, and everyone wears multiple hats, Brooks said.
“You have to be agile and learn quickly. We’re doing something that’s never been done before. There is no playbook, no coursework to review to do this well.”
Everyone steps up
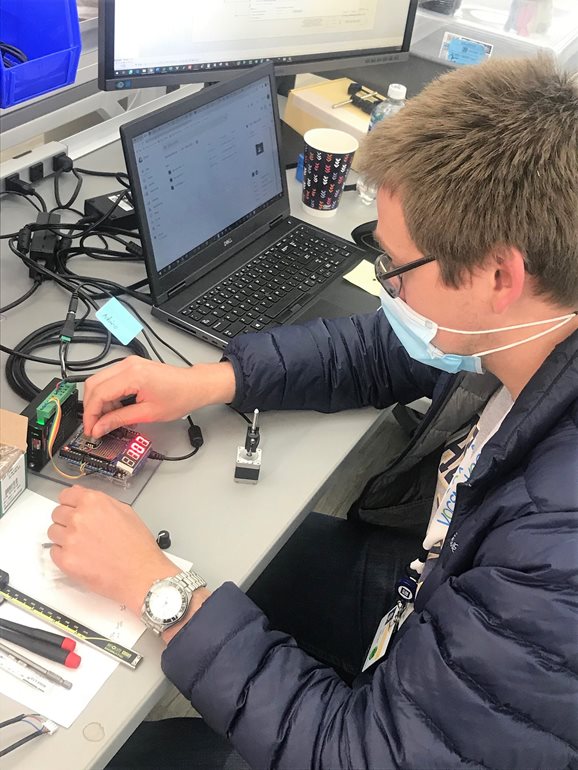
Chapman, Johnson and Sohlberg all know each other from their engineering courses at UW Bothell.
Chapman:
A mechanical design engineer who helped reconfigure VOCSN for production in Kokomo, said that Professor Mourad, who also is a neurological surgery professor at the UW in Seattle, helped prepare students like him who wanted to work in a medical environment. Associate Professor Bridge knew Ventec was looking for an intern and recommended Chapman for the job.
In general, Chapman said, UW Bothell “taught me how to learn” — problem solving, keeping an open mind and sticking with things “when it’s not necessarily fun or easy.”
Now, as a member of the School of STEM’s Mechanical Engineering Advisory Board, Chapman is an advocate of more student projects with rapid prototyping iterations.
Johnson:
A design engineer, he has taken on multiple responsibilities for manufacturing and engineering support in Kokomo. A sense of camaraderie makes long hours more bearable, he said. “Everyone is in it together. It’s not hard to come in and put in the time.”
Johnson said his undergraduate research with Mourad, particularly a capstone project in which his team built a 3D printer that used chocolate, turned out to be valuable.
“Obviously a much smaller scale, but it prepared me for that level of thinking — how to coordinate between people of different disciplines — a cross-functional approach to a complex problem. That was one of the biggest takeaways that has helped me,” said Johnson, who added that lab manager Owen gave him individual assistance.
Sohlberg:
As a prototype engineer, develops product ideas and manufacturing techniques. In Kokomo, he was on the night shift, resolving issues that arose from part variations and assembly-line processes.
Sohlberg said UW Bothell was a good learning environment, with professors such as Collins and Mourad taking time to answer student questions. He also particularly values the problem-solving experience he had in a capstone project building a biodigester.
Taing
Working at Ventec since June of 2019, he expects to continue until he graduates from UW Bothell in 2021, although he eventually hopes to work in the aerospace industry. Taing tests software and hardware — including the Kokomo model — to verify performance and make sure they’re “up to spec.”
He said Professor Mourad structures learning similar to a business experience.
“UW Bothell has a collaborative and project-based atmosphere, which has helped me adapt very well,” Taing said. “UW Bothell makes sure we have all the tools.”
Watch videos of the event with Vice President Mike Pence, Andy Chapman’s comments and his meeting with Pence.